Abstract: The main purpose of this article is to describe the benefits of using an FPGA as a component in a digital controller. For this purpose, various current control techniques for DC motor drives have been designed and implemented. They include a switching current controller, a proportional integral current controller, and a predictive current controller. The quality of this current control is significantly improved, which is critically dependent on the reduction in the delay time of execution. In fact, in all of the above mentioned techniques, the hardware execution time of the design is only a few microseconds. This reduction in time is directly attributable to the FPGAs that may be available and this very powerful dedicated design structure. A large number of experiments have been obtained to illustrate the efficiency of high control performance achieved by FPGA-based solutions in electronic design systems.
Glossary
In the past 20 years, the electronic industry control system has become the focus of important research, and has also made a lot of significant progress and development [1], [2]. These advances and developments are mainly due to the technological revolution, which brought about the production of many powerful devices and the birth of more and more complex algorithms. Based on the successful improvement of the reliability and performance of digital technology, digital control technology has an advantage in the comparison of similar analog devices. In fact, digital control offers many advantages over traditional analog control techniques, such as the flexibility to modify the design to accommodate different systems and environments, immunity to interference, and immunity to component variations. In today's society, most of digital control technology is implemented with microprocessors or DSPs, mainly because of the flexibility of its software and its low price. Therefore, many engineers believe that DSP controller is a more suitable choice [3]. Its component ALU operator is especially used for real-time calculations. It also integrates peripheral modules such as analog-to-digital converters and timers for the drive of electronic systems. However, some of the advantages of analog control are still difficult to replace, such as accuracy, and most importantly the delay of the feedback loop. In fact, although multiprocessor designs or high performance DSP processors can handle these problems, they are still limited in the complexity of the algorithm structure, while at the same time they cost more than the benefits [ 4].
In order to advance the performance of the controller and thereby reduce the gap between the analog world and the digital world, FPGA is considered to be a more suitable option [5]. Take the fast ADC, although the FPGA is running under complex algorithms, but it only takes a few microseconds of real-time computing time. On the other hand, FPGAs can allow adaptive control structures to perform instantaneous free-position sampling [8], [9]. At the same time, FPGAs allow different control functions to be implemented in a fully integrated system-on-a-chip (SOC) [5]-[7]. Therefore, the application of FPGA in electronic drive is very mature. It has been successfully applied to the control of PWM converters [10], motor drives [11], [12], and even multi-machine control systems. To further illustrate, like a DSP controller, the components of an FPGA are also very low cost. Recently, a company has even introduced one such FPGA family, which includes several analog functions, such as ADC [14].
Therefore, in order to combine these advantages and some of the new advantages presented, this paper systematically describes an FPGA-based current controller for use in AC motor drive. These industrial applications are examples of high-level real-time performance in industrial control systems.
The first is to use FPGA technology in the switch current controller. On this basis, a comprehensive analysis of the two sets of controllers, the first group is characterized by a variable switching frequency, while the second group is based on a limited switching frequency. The use of FPGA-based controllers can greatly improve the quality of current waveforms, depending on their extremely short execution time. The digital controllers obtained under these conditions can be approximated to their corresponding analog controllers.
The following is a comprehensive description of a proportional integral (PI) current controller. It has now been proven to contribute to instantaneous free-position sampling, which can increase control performance. It should be noted that the extremely short execution time allows the development of an asynchronous PWM strategy, which means that the reference voltage is continuously refreshed at a high sampling frequency (up to 200 kHz), which is useful for high power applications requiring low switching frequency. Great benefit.
After that, the implementation and development of FPGA in synchronous motor current prediction controller are stated. As we all know, current prediction controllers require complex planning budgets [15]–[18]. Therefore, the feature of the current prediction controller that is digitized is that there must be a delay between the current sensing instant and the moment when the voltage vector in the applicable voltage source inverter (VSI) is about to be applied. In this case, the performance of the controller is greatly dependent on the calculation time, for which the calculation time must be sufficiently shorter than the sampling period [19]. Therefore, if the calculation time is not short enough, then a complex modulation algorithm is needed to guarantee the basic performance level of the controlled system [20], [21]. The proposed FPGA-based current prediction controller ensures real-time voltage vector calculation without adding any modulation algorithms. In this case, the entire execution time (including AD conversion) is only 4.52 microseconds.
However, in order to achieve a high level of control performance, only the most important design efforts can be relied upon. This is why I proposed a special part of the applicable design methodology based on FPGA. It comes from two compromises that need to be reversed. The two needs are: 1) a friendly design environment that does not threaten non-microelectronics professional designers; 2) a comprehensive consideration of control performance needs.
All of the studied current controllers were tested under the experimental setup shown in Figure 1. The general structure of all current controllers includes the current controller itself, the ADC, the DA conversion interface, and the RS232 serial universal asynchronous receive/transmit (UART) interface, which together form a complete system-on-a-chip (SOC).
A large number of experimental results demonstrate the benefits and effectiveness of the proposed FPGA-based current controller.
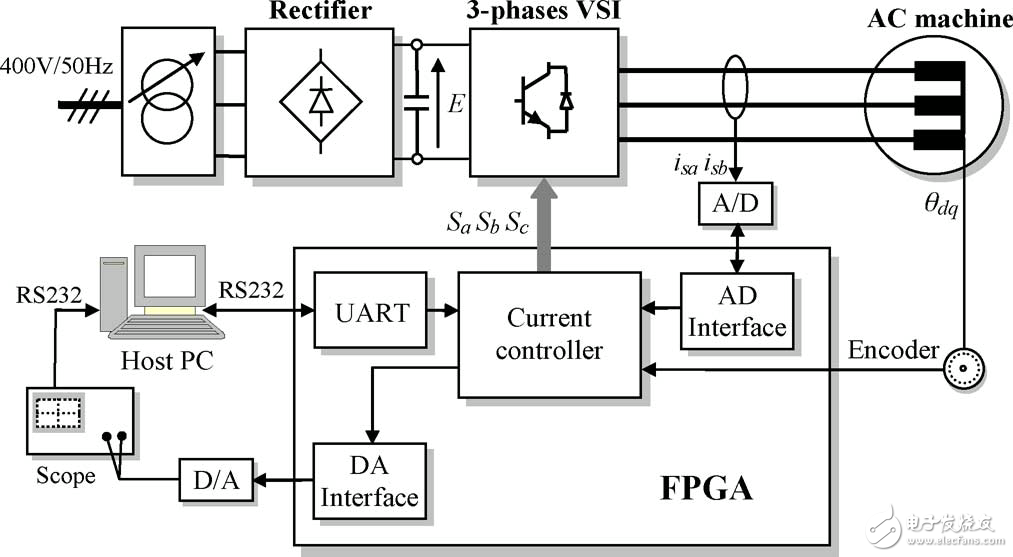
[2] MP Kazmierkowski, R. Krishnan, and F. Blaabjerg, Control in Power Electronics: Selected Problems. Norwell, MA: Academic, 2002.
[3] C. CecaTI, "Microprocessors for power electronics and electrical drives applicaTIons," IEEE Ind. Electron. Soc. Newslett., vol. 46, no. 3, pp. 5–9, Sep. 1999.
[4] S. Berto, A. Paccagnella, M. Ceschia, S. Bolognani, and M. Zigliotto, "PotenTIals and pitfalls of FPGA application in inverter drives - A case study," in Proc. IEEE ICIT, Maribor, Slovenia, Dec.2003, pp.500–505.
[5] E. Monmasson and YA Chapuis, "Contributions of FPGA's to the control of electrical systems, A review," IEEE Ind. Electron. Soc. Newslett., vol. 49, no. 4, pp. 8–15, Dec. 2002.
[6] X. Lin-Shi, F. Morel, A. Llor, B. Allard, and J.-M. Retif, "Implementation of hybrid control for motor drives," IEEE Trans. Ind. Electron, vol. No.4, pp.1946–1952, Aug. 2007.
[7] J. Acero, D. Navarro, L.-A. Barragán, I. Garde, J.-I. Artigas, and J.-M. BurdÃo, "FPGA-based power measuring at induction heating appliances using sigma- Delta A/D conversion," IEEE Trans. Ind. Electron, vol. 54, no. 4, pp. 1843 - 1852, Aug. 2007.
[8] A. Fratta, G. Griffero, and S. Nieddu, "Comparative analysis among DSP and FPGA-based control capabilities in PWM power converters," in Proc. IEEE IECON, Busan, Korea, Nov. 2004, pp. 257 –262.
[9] F. Blaabjerg, PC Kjaer, PO Rasmussen, and C. Cossar, "Improved digital current control methods in switched reluctance motor drives," IEEE Trans. Power Electron., vol. 14, no. 3, pp. 563-572, May 1999.
[10]Y.Tzou and H.-J.Hsu, "FPGA realization of space-vector PWM control IC for three-phase PWM inverters," IEEE Trans. Power Electron., vol.12, no.6, pp.953 –963, Nov.1997.
[11] M.-W. Naouar, E. Monmasson, and I. Slama-Belkhodja, "FPGA-based torque controller of a synchronous machine," in Proc. IEEE ICIT, Hammamet, Tunisia, Dec. 2004, pp. –10.
[12] Y.-A. Chapuis, C. Giredd, F. Aubépart, J.-P. Blonddé, and F. Braun, "Quantization problem analysis on ASIC-based direct torque control of an induction machine," in Proc. IEEE IECON, Aachen, Germany, Sep. 1998, pp. 1527–1532.
[13] K. Tazi, E. Monmasson, and J.-P. Louis, "Description of an entirely reconfigurable architecture dedicated to the current vector control of a set of AC machines," in Proc. IEEE IECON, San Jose, CA , Nov. 1999, pp. 1415–1420.
[14] Actel, Data Book, 2006. [Online].Available:
[15] R. Kennel and A. Linder, "Predictive control of inverter supplied electrical drives," in Proc. IEEE PESC, Jun. 2000, pp. 761–766.
[16] J. Holtz and S. Stadtfeld, "A predictive controller for the stator current vector of AC machines fed from a switched voltage source," in Proc. IPEC, Tokyo, Japan, 1983, pp. 1665–1675.
[17] J. Holtz and S. Stadtfeld, "A PWM inverter drive system with online optimized pulse patterns," in Proc. EPE Conf., Brussels, Belgium, Sep. 1985, pp. 321-325.
[18] H. Le-Huy, K. Slimani, and P. Viarouge, "Analysis and implementation of a real-time predictive current controller for permanent-magnet synchronous servo drives," IEEE Trans. Ind. Electron., vol. , no.1, pp.110–117, Feb. 1994.
[19] DC Lee, SKSul, and MH Park, "High performance current regulator for a field-oriented adaptive induction motor drive," IEEE Trans. Ind. Appl., vol. 30, no. 5, pp. 1247–1257, Sep. /Oct.1994.
[20] O. Kukrer, "Discrete-time current control of voltage-fed three phase PWM inverter," IEEE Trans. Power Electron., vol. 11, no. 2, pp. 260-269, Mar. 1996.
[21] H.-T. Moon, H.-S. Kim, and M.-J. Youn, "A discrete time predictive current control for PMSM," IEEE Trans. Power Electron., vol. 18, no. , pp.464–472, Jan. 2003.
Gaming Headphones is a headset suitable for playing games. For game users, a game headset with excellent performance can allow players to experience the immersive feeling in the game. For competitive game players, the game headset can also assist game players and enhance combat effectiveness.
In the case of headphone use, we found that game use would be a large part of the demand, especially the need to use a pure headset to get better listening effect when both music and games are in use.
Compared with music headphones, Wired Game Headphones pay more attention to sound field and positioning sense (for example, shooting and shootout games need positioning), and the amount and intensity of low frequency are aggravated, so as to meet the user's experience of game sound effects. Music headphones, in essence, pay more attention to sound quality. The effect in the right range is super good, with pure sound quality and penetrating sound.
Among the many headsets, Wireless Gaming Headphone have the advantage of sensitivity. The relatively closed listening environment is also more conducive to game players to feel the details of the sound and improve their judgment of the sound. Therefore, compared with traditional headsets, gaming headsets have more advantages in positioning ability, can better express the sense of direction of sound, and are more suitable for 3D games to express sound clearly. In addition, player-oriented game headsets are often enhanced with low-frequency volume sensing to facilitate the game's plot and make it easier for players to immerse themselves in the game.
Gaming Headphones,Gaming Headset,Rgb Gaming Headphones,Gaming Bluetooth Earphones
Henan Yijiao Trading Co., Ltd , https://www.yjusbhubs.com